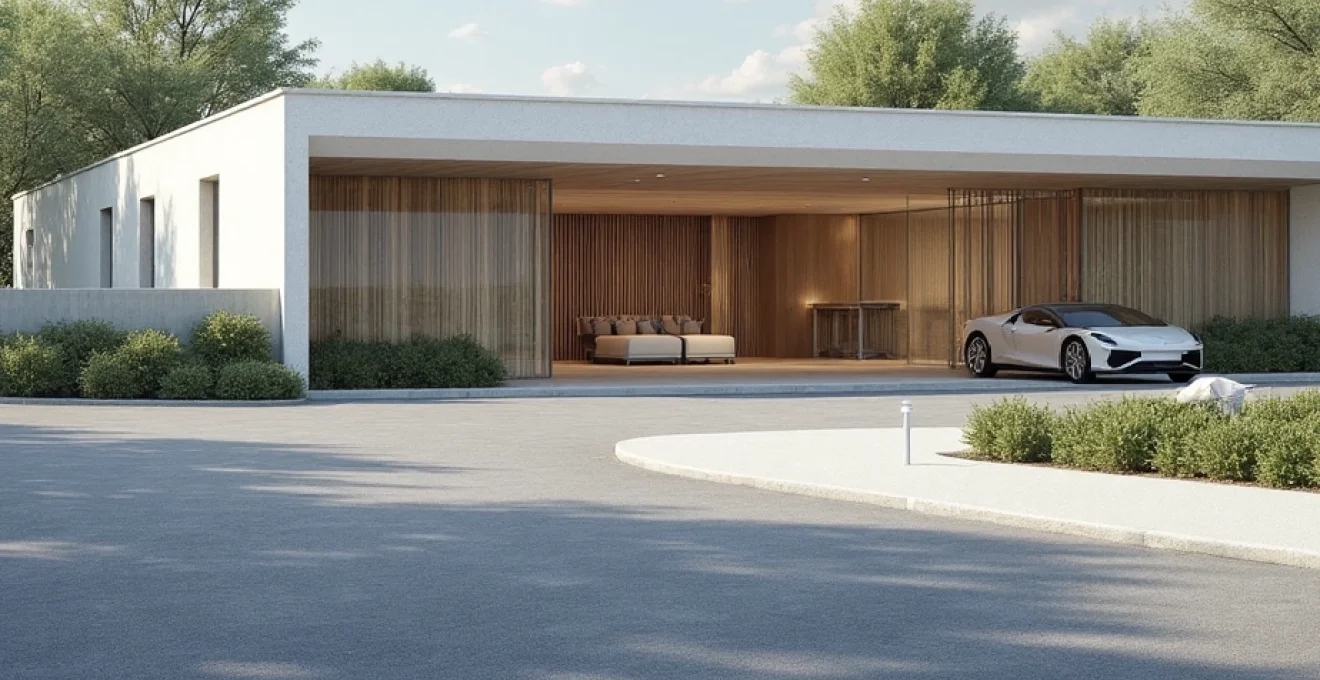
L’arrimage sécurisé des charges est un élément crucial dans le domaine du transport et de la logistique. Que ce soit pour stabiliser des structures temporaires ou sécuriser des marchandises pendant leur acheminement, l’utilisation de gueuses et de contrepoids joue un rôle fondamental. Ces dispositifs, souvent méconnus du grand public, sont pourtant essentiels pour garantir la sécurité et l’efficacité des opérations de transport et de manutention. Comprendre leurs principes mécaniques, les différents types disponibles et les techniques d’utilisation appropriées est indispensable pour tout professionnel du secteur.
Principes mécaniques des gueuses et contrepoids
Les gueuses et contrepoids fonctionnent sur un principe mécanique simple mais efficace : l’exploitation de la force gravitationnelle. En ajoutant une masse significative à un point stratégique, ces dispositifs créent une force opposée au mouvement indésirable de la charge ou de la structure à stabiliser. Cette opposition aux forces externes, qu’elles soient dues au vent, aux vibrations ou aux mouvements du véhicule, permet de maintenir l’équilibre et la stabilité du système.
La clé de l’efficacité d’une gueuse ou d’un contrepoids réside dans son poids et sa position. Plus la masse est importante et placée judicieusement, plus la force de maintien sera conséquente. Cependant, il est crucial de trouver le juste équilibre entre le poids nécessaire pour assurer la stabilité et les contraintes pratiques liées à la manipulation et au transport de ces éléments.
Le concept de bras de levier joue également un rôle prépondérant dans l’efficacité des contrepoids. En augmentant la distance entre le point d’ancrage et le centre de gravité du contrepoids, on amplifie son effet stabilisateur. Cette compréhension permet d’optimiser la conception et le positionnement des systèmes d’arrimage pour une efficacité maximale.
Types de gueuses et matériaux adaptés à l’arrimage
Le choix du type de gueuse ou de contrepoids dépend grandement de l’application spécifique et des contraintes environnementales. Chaque matériau présente des avantages et des inconvénients qu’il convient de peser soigneusement pour sélectionner la solution la plus adaptée à chaque situation.
Gueuses en fonte : résistance et densité optimales
Les gueuses en fonte sont parmi les plus populaires dans l’industrie de l’arrimage. Leur densité élevée permet d’obtenir un poids important dans un volume relativement restreint. La fonte offre également une excellente résistance à la corrosion et aux chocs, ce qui en fait un choix durable pour des utilisations intensives ou en environnements difficiles.
La malléabilité de la fonte permet de créer des formes variées, adaptées à différents types d’ancrage ou de fixation. On trouve ainsi des gueuses en forme de parallélépipède, de cylindre ou même avec des poignées intégrées pour faciliter leur manipulation. Cette versatilité rend les gueuses en fonte particulièrement appréciées dans les secteurs maritimes et industriels.
Contrepoids en béton : fabrication et applications
Le béton représente une alternative économique et largement disponible pour la fabrication de contrepoids. Sa densité, bien que moindre que celle de la fonte, reste suffisante pour de nombreuses applications. Les contrepoids en béton sont souvent utilisés dans le domaine de la construction, notamment pour stabiliser des grues ou des échafaudages.
L’un des principaux avantages du béton est la possibilité de le couler sur place, permettant ainsi de créer des contrepoids sur mesure adaptés à des configurations spécifiques. De plus, l’ajout d’armatures métalliques peut considérablement augmenter la résistance mécanique du béton, le rendant apte à supporter des contraintes importantes.
Alternatives modernes : polyéthylène et composites
Les avancées technologiques ont permis l’émergence de nouveaux matériaux pour la fabrication de gueuses et contrepoids. Le polyéthylène haute densité (PEHD) et les matériaux composites offrent des solutions innovantes combinant légèreté et résistance.
Ces matériaux présentent l’avantage d’être facilement transportables et manipulables, tout en offrant une bonne résistance aux intempéries et aux produits chimiques. Ils sont particulièrement adaptés pour des applications temporaires ou mobiles, où la facilité de mise en place et de retrait est primordiale.
Critères de sélection selon l’environnement d’utilisation
Le choix du matériau pour une gueuse ou un contrepoids doit prendre en compte plusieurs facteurs environnementaux. Dans un milieu marin, par exemple, la résistance à la corrosion sera un critère déterminant, favorisant l’utilisation de matériaux comme l’acier inoxydable ou certains composites. Pour des applications en intérieur ou dans des zones sensibles aux rayures, des matériaux plus doux comme le caoutchouc ou le polyéthylène seront privilégiés.
La fréquence de déplacement des contrepoids est également un facteur à considérer. Pour des installations fixes à long terme, des matériaux lourds comme la fonte ou le béton sont souvent préférés. En revanche, pour des utilisations nécessitant des déplacements fréquents, des solutions plus légères et ergonomiques seront plus appropriées.
Techniques d’arrimage sécurisé avec gueuses
L’efficacité de l’arrimage ne dépend pas uniquement du choix du contrepoids, mais aussi de la technique employée pour le mettre en place. Une approche méthodique et réfléchie est essentielle pour garantir la sécurité et la stabilité de la charge arrimée.
Méthode d’ancrage à point fixe pour structures légères
Pour les structures légères comme les tentes ou les barnums, une méthode d’ancrage à point fixe est souvent suffisante. Cette technique consiste à attacher directement la gueuse aux points d’ancrage de la structure à l’aide de sangles ou de cordes. L’objectif est de créer une tension constante qui maintient la structure en place, même en cas de vent modéré.
Il est crucial de répartir uniformément les points d’ancrage autour de la structure pour assurer une stabilité optimale. La règle d’or est de placer au moins une gueuse à chaque coin et au milieu de chaque côté pour les structures rectangulaires . Pour les structures circulaires, une disposition en étoile avec des gueuses espacées régulièrement est recommandée.
Système de répartition de charge pour grandes surfaces
Lorsqu’il s’agit d’arrimer des charges de grande surface, comme des bâches ou des panneaux publicitaires, un système de répartition de charge est plus approprié. Cette méthode utilise un réseau de sangles ou de câbles pour distribuer la force de retenue sur l’ensemble de la surface.
La clé de cette technique réside dans la création d’un maillage équilibré. Les gueuses sont placées à intervalles réguliers le long du périmètre de la surface à arrimer, puis reliées entre elles par un système de sangles croisées. Cette configuration permet de répartir uniformément la tension et d’éviter les points de faiblesse où le vent pourrait s’engouffrer.
Arrimage dynamique : adaptation aux conditions variables
Dans certains environnements, les conditions peuvent changer rapidement, nécessitant un système d’arrimage capable de s’adapter. L’arrimage dynamique utilise des dispositifs comme des tendeurs à ressort ou des systèmes hydrauliques pour maintenir une tension constante malgré les variations de charge ou les mouvements de la structure.
Cette approche est particulièrement utile dans le transport maritime, où les mouvements du navire peuvent affecter la stabilité de la cargaison. Des systèmes d’arrimage dynamique bien conçus peuvent absorber les chocs et les vibrations, réduisant ainsi le risque de dommages aux marchandises transportées .
Utilisation de tendeurs et sangles haute résistance
La qualité des équipements d’arrimage est tout aussi importante que la méthode employée. L’utilisation de tendeurs et de sangles haute résistance est essentielle pour garantir la sécurité de l’arrimage. Ces équipements doivent être capables de supporter non seulement le poids de la charge, mais aussi les forces dynamiques générées pendant le transport ou en cas de conditions météorologiques défavorables.
Il est recommandé d’utiliser des sangles certifiées selon les normes en vigueur, comme la norme EN 12195-2
pour les sangles d’arrimage en textile. Les tendeurs doivent être choisis en fonction de leur capacité de charge maximale (CMU) et de leur résistance à la rupture. Un facteur de sécurité d’au moins 2:1 entre la résistance à la rupture et la charge maximale d’utilisation est généralement conseillé.
Calcul et dimensionnement des contrepoids
Le dimensionnement correct des contrepoids est crucial pour assurer l’efficacité et la sécurité de l’arrimage. Un calcul précis permet d’éviter le surdimensionnement, qui entraînerait des coûts et des difficultés de manipulation inutiles, tout en garantissant une marge de sécurité suffisante.
Formules de calcul de la force de retenue nécessaire
Pour déterminer le poids nécessaire d’un contrepoids, il faut d’abord calculer la force de retenue requise. Cette force dépend de plusieurs facteurs, notamment le poids de la charge à arrimer, les forces dynamiques prévisibles (vent, accélération, etc.) et le coefficient de frottement entre la charge et la surface de support.
Une formule simplifiée pour calculer la force de retenue minimale (F) peut s’exprimer ainsi :
F = m * g * (μ + a/g)
Où :
- m est la masse de la charge en kg
- g est l’accélération due à la gravité (9,81 m/s²)
- μ est le coefficient de frottement statique
- a est l’accélération maximale prévue en m/s²
Cette formule de base doit être ajustée en fonction des conditions spécifiques d’utilisation et des normes en vigueur dans le secteur concerné.
Logiciels spécialisés : ANSYS et SOLIDWORKS pour la simulation
Pour des calculs plus complexes, notamment dans le cas de structures ou de charges non standard, l’utilisation de logiciels de simulation devient indispensable. Des outils comme ANSYS ou SOLIDWORKS permettent de modéliser précisément les contraintes et les forces en jeu, offrant ainsi une analyse plus fine et fiable.
Ces logiciels utilisent la méthode des éléments finis pour simuler le comportement des structures sous différentes conditions de charge. Ils peuvent prendre en compte des facteurs comme la géométrie complexe des pièces, les propriétés des matériaux et les interactions entre différents composants du système d’arrimage.
Facteurs de sécurité et marges de tolérance recommandées
Dans la pratique, il est essentiel d’appliquer des facteurs de sécurité appropriés aux calculs théoriques. Ces facteurs permettent de compenser les incertitudes liées aux conditions réelles d’utilisation, aux variations de qualité des matériaux et aux éventuelles erreurs de calcul ou de manipulation.
Les facteurs de sécurité recommandés varient selon le domaine d’application et les normes en vigueur. Dans le transport routier, par exemple, un facteur de sécurité de 1,5 à 2 est couramment utilisé . Pour des applications plus critiques ou dans des environnements plus contraignants, des facteurs de sécurité plus élevés, allant jusqu’à 3 ou 4, peuvent être nécessaires.
Réglementation et normes d’arrimage
L’arrimage des charges est soumis à une réglementation stricte visant à garantir la sécurité des opérations de transport et de manutention. Ces normes et directives évoluent régulièrement pour s’adapter aux nouvelles technologies et aux retours d’expérience du terrain.
Directive européenne 2014/47/UE sur le contrôle technique
La directive européenne 2014/47/UE établit un cadre pour le contrôle technique des véhicules utilitaires circulant dans l’Union européenne. Cette directive inclut des dispositions spécifiques concernant l’arrimage des charges, soulignant l’importance de cette pratique pour la sécurité routière.
Selon cette directive, les autorités compétentes sont tenues de vérifier que l’arrimage des charges respecte les normes de sécurité en vigueur. Cela implique des contrôles sur l’état des équipements d’arrimage, la répartition de la charge et l’adéquation des méthodes utilisées par rapport au type de marchandises transportées.
Norme ISO 27956 pour l’arrimage des charges
La norme ISO 27956 fournit des lignes directrices pour l’arrimage des charges dans les véhicules routiers. Elle définit les exigences et les méthodes d’essai pour les dispositifs d’arrimage, ainsi que les recommandations pour leur utilisation correcte.
Cette norme couvre divers aspects, notamment :
- Les spécifications techniques des points d’ancrage
- Les méthodes de calcul des forces d’arrimage
- Les procédures de test pour les équipements d’arrimage
- Les recommandations pour la formation des opérateurs
Le respect de la norme ISO 27956 est crucial pour assurer la conformité des opérations d’arrimage aux standards internationaux de sécurité .
Certifications et agréments requis pour les systèmes d’arrimage
Les équipements d’arrimage doivent être certifiés conformes aux normes en vigueur. Ces certifications garantissent que le matériel a été testé et approuvé pour résister aux contraintes spécifiques de l’arrimage.
Parmi les certifications importantes
, on trouve notamment :
- Le marquage CE pour les équipements commercialisés dans l’Union européenne
- La certification LC (Lashing Capacity) qui indique la capacité maximale d’arrimage
- L’agrément VDI pour les systèmes d’arrimage en Allemagne
- La certification GS (Geprüfte Sicherheit) attestant de la sécurité testée
Il est crucial de vérifier que tous les équipements utilisés pour l’arrimage possèdent les certifications appropriées et sont conformes aux réglementations en vigueur dans la zone d’utilisation.
Maintenance et inspection des systèmes d’arrimage
La fiabilité des systèmes d’arrimage dépend grandement de leur entretien régulier et de leur inspection minutieuse. Une maintenance préventive permet non seulement de prolonger la durée de vie des équipements, mais aussi de garantir leur efficacité et la sécurité des opérations.
Protocoles d’inspection visuelle et tactile
L’inspection visuelle et tactile est la première ligne de défense contre les défaillances des systèmes d’arrimage. Ces contrôles doivent être effectués avant chaque utilisation et de manière plus approfondie à intervalles réguliers.
Lors d’une inspection visuelle, il convient de rechercher :
- Des signes d’usure excessive ou d’effilochage sur les sangles
- Des déformations ou fissures sur les crochets et les tendeurs
- Des traces de corrosion sur les parties métalliques
- Des dommages aux points d’ancrage
L’inspection tactile complète l’examen visuel en permettant de détecter des anomalies non visibles à l’œil nu, comme des rugosités inhabituelles ou des zones de faiblesse dans les matériaux.
Tests de charge statique et dynamique
Au-delà des inspections visuelles et tactiles, des tests de charge sont essentiels pour vérifier l’intégrité structurelle des systèmes d’arrimage. Ces tests simulent les conditions réelles d’utilisation et permettent de détecter des faiblesses qui pourraient passer inaperçues lors d’une simple inspection visuelle.
Les tests de charge statique consistent à appliquer une charge constante sur le système d’arrimage pendant une période déterminée. Ils permettent de vérifier la résistance des matériaux et des points d’ancrage sous une contrainte prolongée.
Les tests de charge dynamique, quant à eux, simulent les forces subies par le système d’arrimage lors des accélérations, freinages et virages. Ces tests sont particulièrement importants pour les équipements utilisés dans le transport routier ou maritime, où les charges sont soumises à des mouvements fréquents.
Fréquence des contrôles selon l’intensité d’utilisation
La fréquence des inspections et des tests doit être adaptée à l’intensité d’utilisation des systèmes d’arrimage. Une règle générale est de procéder à une inspection approfondie et à des tests de charge au moins une fois par an pour les équipements à usage régulier. Cependant, cette fréquence peut être augmentée dans les cas suivants :
- Utilisation intensive (plusieurs fois par jour)
- Exposition à des conditions environnementales difficiles
- Après un incident ou une surcharge
- Lorsque requis par la réglementation spécifique à certains secteurs
Pour les équipements utilisés moins fréquemment, une inspection avant chaque utilisation reste nécessaire, complétée par un contrôle approfondi annuel.
Documentation et traçabilité des opérations de maintenance
La documentation rigoureuse des opérations de maintenance et d’inspection est cruciale pour assurer la traçabilité et démontrer la conformité aux normes de sécurité. Un registre de maintenance doit être tenu pour chaque équipement d’arrimage, incluant :
- Les dates et résultats des inspections
- Les détails des tests de charge effectués
- Les réparations ou remplacements réalisés
- Les incidents éventuels survenus lors de l’utilisation
Cette documentation sert non seulement à suivre l’historique de l’équipement, mais aussi à planifier les maintenances futures et à identifier les tendances pouvant indiquer des problèmes récurrents. De plus, en cas d’incident, ces registres peuvent être cruciaux pour démontrer que toutes les précautions nécessaires ont été prises.
L’utilisation de systèmes de gestion de maintenance assistée par ordinateur (GMAO) peut grandement faciliter la tenue de ces registres, en permettant un suivi en temps réel et des rappels automatiques pour les inspections et maintenances planifiées.
En conclusion, une approche systématique de la maintenance et de l’inspection des systèmes d’arrimage est essentielle pour garantir leur fiabilité et la sécurité des opérations. En combinant des protocoles d’inspection rigoureux, des tests réguliers et une documentation détaillée, les professionnels du transport et de la logistique peuvent minimiser les risques liés à l’arrimage des charges et assurer la conformité aux normes en vigueur.